With the popularity of hybrid and pure electric vehicles, and the active promotion of green new energy vehicles in various countries, the demand for power batteries will increase in size in the future, and the production capacity, efficiency and yield of power batteries will be more and more demanding for major manufacturers. In addition, batteries are also developing in terms of high capacity density, miniaturization, and cost reduction, so stricter quality control is required. The following is the introduction of Qin Taisheng's visual technology applied in the battery intelligent manufacturing industry, which helps the production of power batteries to be intelligent, efficient and high-quality.
Appearance inspection of positive electrode, negative electrode and diaphragm material in battery cell
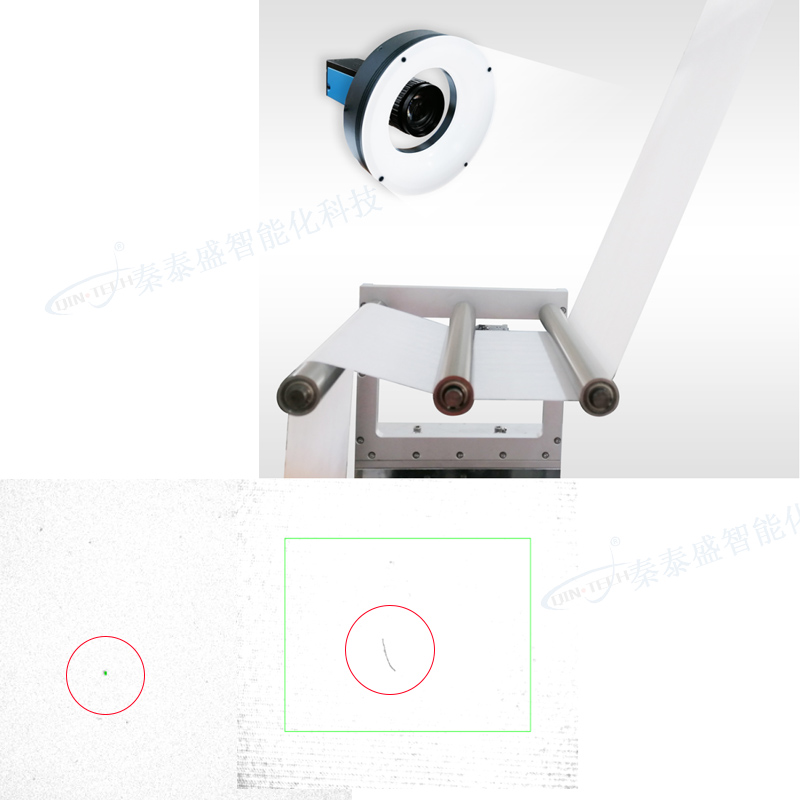
In the production of battery materials, it is necessary to monitor the quality of the materials. Qin Taisheng can monitor the wrinkles, foreign particles, burrs and other defects of the material sheets online through professional visual hardware + self-developed visual processing software.
When the battery pole pieces are stacked, if the pole pieces are offset, it will cause the danger of poor casing insertion or leakage of electrolyte. The position deviation of the pole pieces can be calculated by the Qin Taisheng visual positioning system. The upper computer software can guide the XY modules to stack with high precision; the visual software can take flying pictures, search for the material center, calculate the deviation and compensate for accurate positioning during high-speed operation.
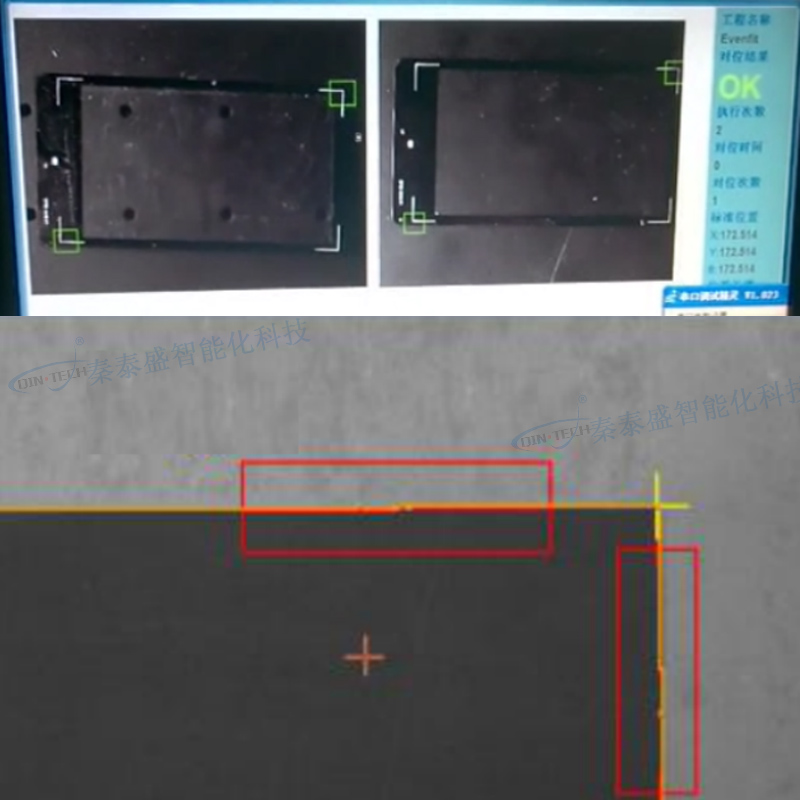
Before the battery cell is inserted into the aluminum case, it can be detected by visual software to ensure that the diaphragm material does not exceed the aluminum case, avoiding the leakage of foreign matter such as the diaphragm, which damages the sealing performance of the battery pack, and avoids the risk of leaking solution.
The Qin Taisheng vision system can be used for the traceability system in production. It can realize the docking data with the customer's MES/SFC and other systems through the upper computer software, so as to achieve the traceability of the products in production.