Equipment hard requirements
1. Automation takes up less space.
2. The entire equipment operation stage must be reliable, and the personal safety of the operators must be guaranteed under the conditions of normal operation.
3. During the reverse winding process of the battery core, if there is a separator, positive electrode and negative electrode fragments, the induction shutdown can be realized, and the reel (pin) can be connected by manual intervention. After the process is sorted out, the machine will automatically continue to the next process.
4. The equipment should be safe and reliable, easy to operate, and the noise should meet the national first-class standard.
Equipment market outlook:
At present, the recycling of used power battery pole cores for new energy vehicles is in the form of smashing and collective recycling. The third-party recycling is carried out in the open air and is naturally decomposed under normal ambient air. In this way, the materials for processing pole cores are not effectively distinguished. Unfavorable factors such as long decomposition time period, large environmental pollution (water, land, air), and many personnel contact.
The key is that the current national strategy guides the public to have a large demand for batteries, and the after-sales recycling and scrapping of battery cores are time-consuming, labor-intensive, and capital-intensive, and there is an urgent expectation for personnel health and environmental protection. Therefore, the internal materials of the battery pole cores are distinguished by different materials, so that the materials of the battery pack pole cores can be separated and reused.
The equipment has the advantages of recycling materials again, environmental protection, less personnel contact, high degree of automation, low energy consumption, etc., which greatly reduces the cost of recycling and processing.
1. Introduction to the device (including a basic introduction to functions):
The new energy power battery pole core is put into the equipment feeding station, and the rewinder completely separates the battery pole core (liquid injection and non-liquid injection battery core) into three parts: positive electrode sheet, negative electrode sheet and diaphragm, and place them separately. The size positioning of the polarized core package, the rewinding transfer mechanism, the protective film attached to the split surface, the negative electrode sheet of the polarized core, the protective film of the polarized core, the positive electrode sheet of the polarized core, the sorting and recycling box, and the safety system. The eight processing functions are: The all-in-one machine performs comprehensive anti-corrosion treatment on the releasable materials of new energy vehicle battery recycling equipment.
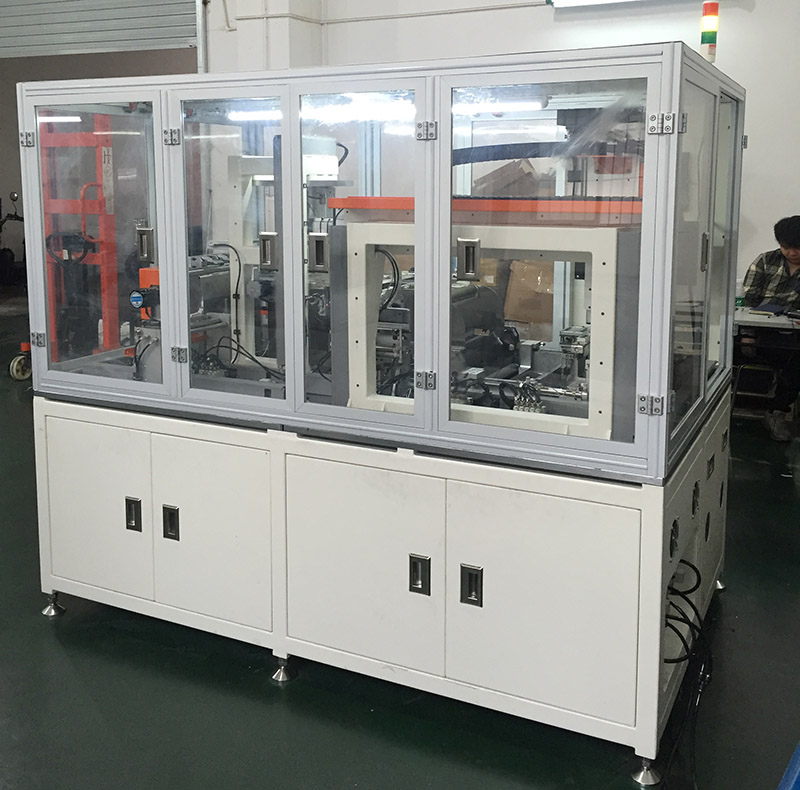
1: Develop an automatic battery pole rewinding machine for square power battery poles (L: 340; W: 140, allowable length and width ±10mm error).
2: The positive electrode sheet of the battery pole core, the negative electrode sheet and the separator are completely separated into a single independent part, and are placed in the designated material box independently for subsequent decomposition.
3: After the diaphragm is wound, it is recycled into the recycling box, and the positive and negative electrodes are recycled into the recycling box respectively.
4: Disassemble the battery in an enclosed space (exhaust pipes are provided on site by the customer).
Process flow:
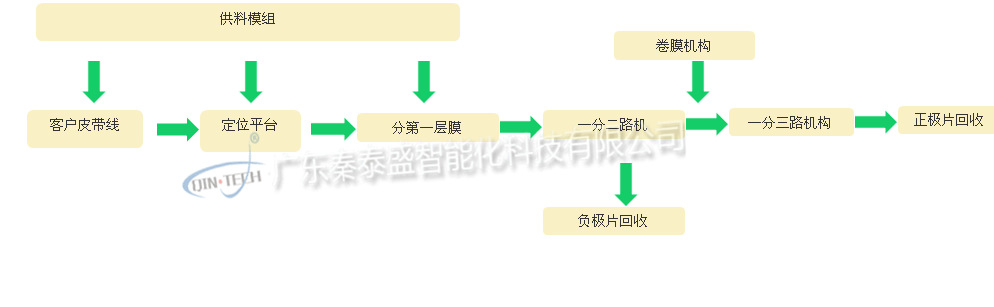
Equipment advantages:
1. Automation takes up less space;
2. During the rewinding process of the battery pole, if the separator, positive electrode and negative electrode are broken, the induction stop can be realized, and the reel (rolling needle) can be connected manually. After the process is sorted out, the machine will automatically continue to the next process. ;
3. The degree of automation and intelligence is quite high, and the straight-through efficiency is high;
4. The equipment is safe and reliable, the operation is simple, and the noise meets the national first-class standard.
Technical Parameter
Equipment Specification Sheet |
Project | Specification |
Machine type | ARM-BAT1 |
Cell size | L:340;W:140 |
Film cutting method | Eager |
Beat | <60S |
Failure rate | <5% |
Air source specification | >5Mpa |
Power Specifications | AC 220v 50Hz |