Category: Industry information
Date: 2024-11-02
Click: 758
Author: 秦泰盛
Collection:
Qin-Tech automated production line for swell-pad: high efficiency and precision, leading the new trend of the industry
In the context of today's industrial production pursuing high efficiency, precision and intelligence, Qin-Tech's automated production line for swell-pad has become a bright star in the industry with its excellent performance and innovative technology.
The first equipment of this production line is the automatic loading machine, which bears an important starting task. Its role is to deliver large sheets of insulation panels to be cut accurately and precisely to the automated line, where they pass through a belt conveyor line, laying the foundation for the subsequent processing stages.
The panels are then transferred to a second flattening and shaping machine. Here, the panels are carefully shaped to ensure that they are optimally flat and ready for precise cutting. Once the shaping is complete, the insulation boards are again transported via a belt line to a third cutting machine. With special molds and edited programs, the cutting machine cuts the insulation boards into the actual size of the core material of the insulation sheet required by the customer, with a high degree of precision.
Immediately after that, the fourth core material lowering machine comes into play. By means of suction cups, it carries the small pieces of core material to two belt lines in turn, and then transports them to the two PET assembly machines, which are even more exquisite, after a series of complex assembly processes such as automatic PET loading, core material loading, wrapping of long edges, folding of corners, and wrapping of short edges, etc., so as to make the structure of the insulation sheet more stable.
The two PET assembly machines sequentially take the assembled heat insulation sheets in groups of 6 (the number of products can be customized according to the customer's production capacity requirements), and the whole is transported through the 6th hot press loading machine to the 7th hot press machine for vacuum extraction and hot pressing. This process further enhances the quality and performance of the heat insulation sheets.
After hot pressing, the sheet is put into the 9th thickness measuring machine through the 8th hot press unloading machine. Thickness measurement is carried out by high precision contact height sensors to strictly control the product quality. The defective products are put into the defective zone according to the thickness and thinness to ensure that only the good products can continue to flow into the next stage.
The good products then flow into the 10th double-sided adhesive sticker machine for front and back side sticking, and the precision of sticking can be ±0.2mm, fully reflecting the high precision and stability of the production line. After gluing, the heat-insulating sheet flows into the strapping machine through the conveyor line for packing and strapping. After the completion of bundling, it is pushed to the discharging belt line, waiting for manual collection and packing.
With its rigorous process flow, advanced equipment and high automation level, the automated production line of Qin-Tech heat insulation sheet provides a reliable guarantee for the production of heat insulation sheet. In the future, it is believed that this production line will continue to lead the development of the industry and bring efficient and high-quality production solutions to more enterprises.
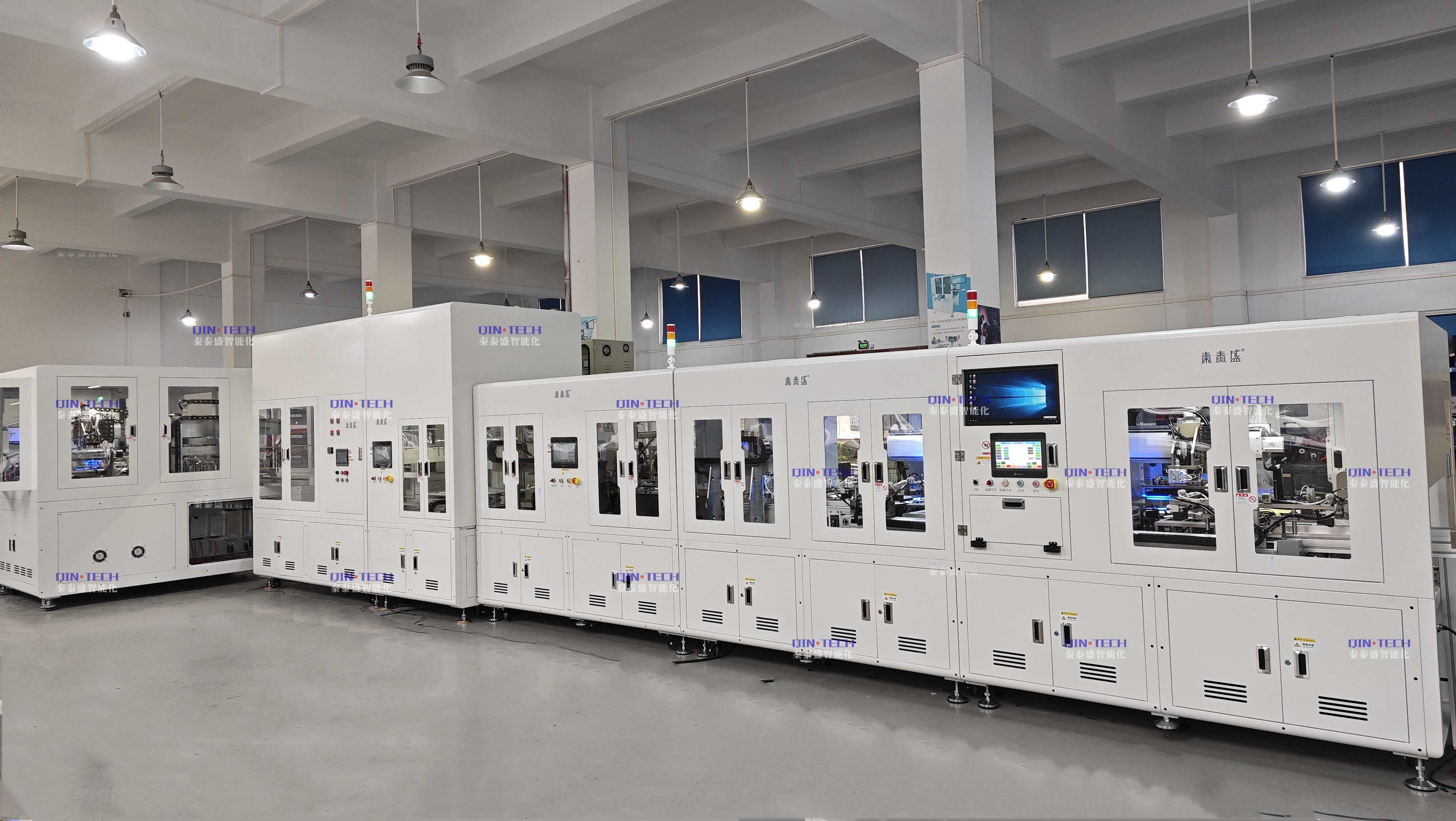